Carbon Steel | Low Allow Steels | 300 Stainless Steels | 400 Stainless Steels | Precipitating-Hardening SS | Aluminum | Copper | Cobalt Base | Nickel Base |
---|---|---|---|---|---|---|---|---|
1020 | 4130 | 302 | 410 | 15-5 PH | A356 | Berrylium Copper | Stellite 6 | Hastealloy B |
1025 | 4140 | 303 | 416 | 17-4 PH | A357 | Stellite 21 | Hastealloy C | |
1040 | 8620 | 304/304L | 431 | Stellite 25 | Hastealloy X | |||
8630 | 316/316L | N155 | Stellite 31 | Iconel 625 | ||||
347 | Monel |
Alloy List
Materials Testing
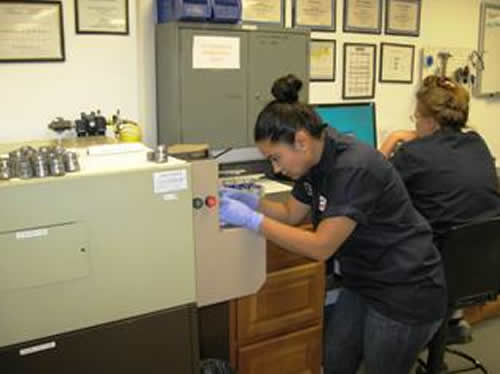
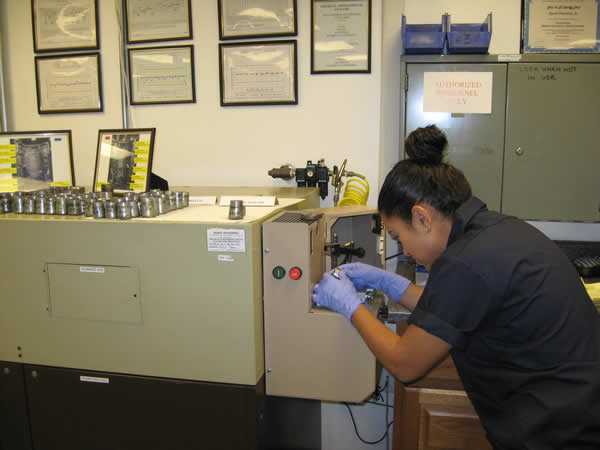
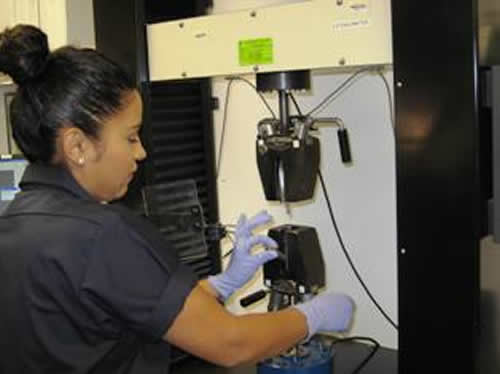
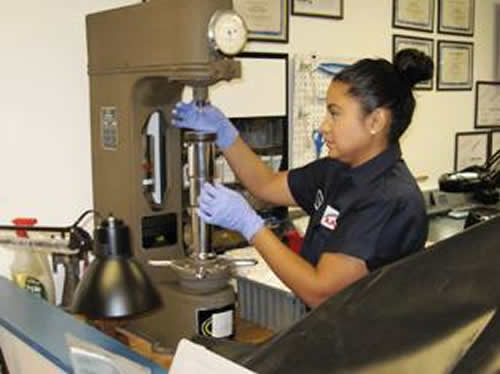
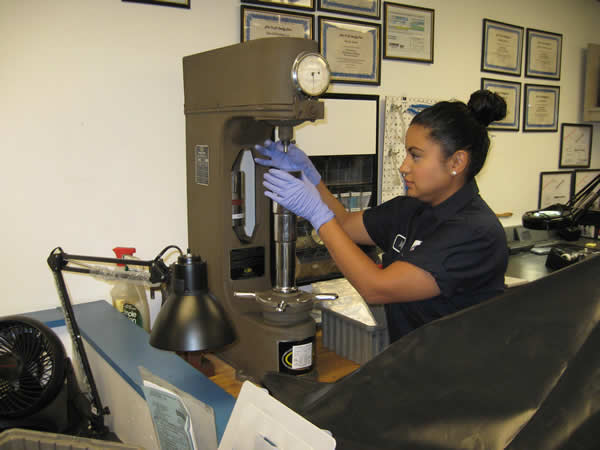
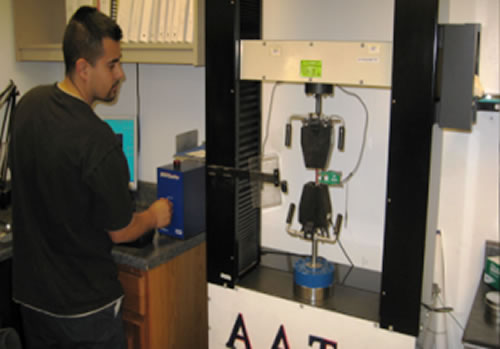
Capabilities & Equipment
CNC
1 HAAS VF 3 SS- 12,000 rpm spindle, through spindle coolant, high pressure coolant, 40” x 20” x25” (X, Y, Z) 4 axis with trunnion (5 axis)
7 HAAS VF 4 SS; Five Axis Machining Centers
1 CNC Matsuura vertical mill 16 inches x 30 inches with 4 x capability up to 14 inches
1 CNC lathe Quasar 250 10 inches x 20 inches with live center
CAD to CAM Programming Capabilities
MILL EQUIPMENT
1 Bridgeport right angle mill heads with rotary tables from 10, 15, 20 inches
1 Bridgeport vertical slotting head
3 Troyke rotary Tables
3 Hardinge universal indexers
4 Bridgeport Mills
LATHE
1 Cadillac engine lathe up to 12 inches hard jaws with 14 x 36 inches table with live center
MISCELLANEOUS EQUIPMENT
1 Haring Precision Surface Graining
1 Sunnen Precision Honing
Non-Destructive Testing
material or system without impairing its future usefulness.
Liquid Penetrant Inspection is performed by applying a flourescent dye to the surface of a non-porus casting to detect cracks or other surface defects.
Magnetic particle inspection is performed by magnetizing castings, and applying iron particles using a wet method, to detect surface and subsurface discontinuities.
X-Ray inspection is performed to ensure that manufactured items meet structure requirements and are free from defects.
Digital Production Definition (DPD)
The electronic elements that specify the 3D Computer Aided Design (CAD) geometry and all design requirements for a product (including notations and parts lists), and the use of this data throughout an integrated CAD Systems, typically consisting of; Computer Aided Manufacturing (CAM); Coordinate Measurement Systems (CMS) and use of Coordinate Measurement Machines (CMM)
Digital Product Definition & CAD CAM
CAD CAM
Purchased MasterCAM software 9/26/13. Capabilities in progress.
Rapid Prototyping
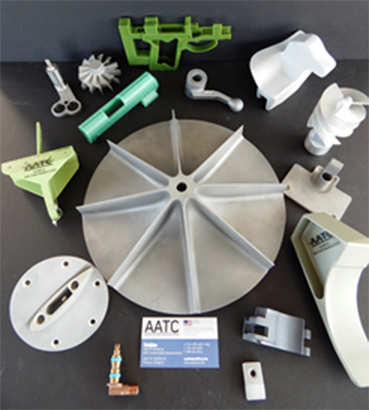
AATC is a leading producer of Rapid Prototype aluminum and steel investment castings
AATC is here to meet all of your Rapid Prototyping needs. We are able to produce castings in as little as 4 weeks by converting patterns using the Stereolithography (SLA) Rapid Prototyping method and eliminating the delays required to manufacture traditional metal tooling. Geometry is virtually limitless and allows for such details as fins, pins, and complex, integrally cast cores. This process is extensively used by design engineers in the development of new products, allowing designers to go directly from a CAD file to a fully functional aluminum and/or steel casting. The method is flexible and allows the use of different RP patterns from a variety of processes.
Traditional Lost-wax Process
The traditional lost-wax process involves the manufacture of a metal tool (die) which typically takes 6-14 weeks depending on part complexity.

Wax is then injected into the die to produce the wax pattern which is subsequently gated and coated with ceramic shell to build a ceramic mold.

The wax pattern is melted out (hence lost wax) and metal is then poured into the empty mold resulting in the casting.

Finished Casting in 10-18 weeks
Rapid Prototype Process
The rapid prototype pattern is built from a CAD design and substituted for the wax pattern. This takes from 1-2 weeks.

The RP pattern is subsequently gated and coated with shell material. After shelling the RP pattern is eliminated from the mold using special procedures.

The remaining production stages follow the traditional lost wax process, producing a finished casting with the rapid prototype pattern.

Finished Casting in 4-5 weeks